So, geht schneller weiter als ich dachte.
Die Lampengrundflächen (nenne ich jetzt mal so) sind dran.
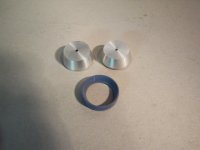
Als Drehteile entstanden zwei Kegelstümpfe aus Alu und ein Formenring.
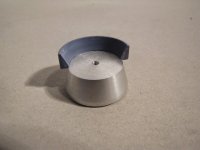
Der Formenring wurde zweigeteilt und mit den Aluteilen verklebt.
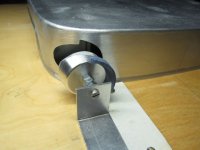
Das Aluteil auf einen Winkel geschraubt. Dieser Winkel und der verschraubte Plastestreifen auf dem Baubrett geben die genaue Position der Lampengrundfläche vor. Ohne so einem Hilfsmittel wäre das im Freihandbauen nie was Genaues geworden.
In das FH wurde dann die Öffnung herausgefräst, geschliffen, gefeilt..., mit vielem Dranhalten, kontrollieren... und wieder schleifen... na ihr wisst schon.
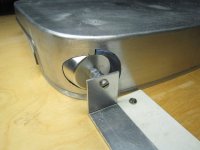
Irgendwann passt das ganze Teil dann auch sauber in das FH. Was jetzt noch an Spalten da ist schließt das angedickte Harz.
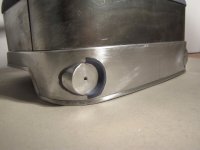
Und so sieht es dann fertig verklebt und verschliffen aus.
Im Original ist das ja alles ein Blechformteil. Deßhalb auch die runden Kanten. Was jetzt noch nicht ganz passend ist gestalte ich nach der Grundierung mit Spachtel. Obwohl ich ja kein Freund von Spachtel bin, aber um hier so eine vielfach gestaltete Form hinzubekommen bleibt Spachtel noch als letztes Mittel. Ist ja auch nur erst mal die Positivform. Die muss nur so lange halten, bis das Negativ abgenommen worden ist.
Ach ja, noch vielen Dank für eure positiven Kommentare.
@ brummbaer, 1:10 ist schon ein toller Maßstab. Man hat richtig was in der Hand, macht in der Größe schon ordentlich was her, die Kosten halten sich noch in Grenzen. Einzig, es gibt auf dem Markt fast nichts an Fertigteilen und Zubehör. Wenn man mal die Offroadszene außen vor lässt. Aber das hat ja mit LKW und ihren Maßen/Abmessungen auch wenig zu tun.
Naja, ich baue ja eh lieber selbst, ob es da einen Anbieter gibt oder nicht.
Gruss Micha