FamoPabst
New member
- Registriert
- 28.09.2017
- Beiträge
- 15
Hallo Trucker,
der Famo, die größte Halbkettenzugmaschine des 2. Weltkrieges, hat mich von dem Moment an fasziniert, als ich vor vielen Jahren den Karton des Tamiya 1/35 Kits auf der Modell Hobby Spiel in Leipzig gesehen habe. Was macht man als junger und unerfahrener Modellbauer? Man sucht sich ein kompliziertes Vorbild und möchte dieses mit ambitionierten Ansprüchen als Modell bauen. Diese Voraussetzungen waren bei mir erfüllt und so beschloss ich, den Famo zu bauen.
Ein Langzeitprojekt ist es jetzt bereits und es wird sicher noch eines für die Zukunft bleiben. Mich stört das aber gar nicht so sehr da die Zeit auch für mich arbeitet - wenn ich nur an die vielen neuen Möglichkeiten denke, die uns Modellbauern nun zur Verfügung stehen...
Bis jetzt gab es grob 3 Phasen des Projektes.
Phase 1: Um 2007 herum. Ich wollte den Famo in 1:16 bauen damit er zu meinem Tamiya Tiger I passt. Ich habe einige 3D-Modelle erstellt. Außerdem habe ich mir eine Fräsmaschine zugelegt(RC-Machines Variante der Rotwerk-Baumarktfräse) Die Kettenglieder wollte ich mit einer selbstgebauten Schleudergussapperatur aus Zamak5 in Silikonform gießen. Den Prototypen dafür habe ich aus Messing gefräst und gelötet.
Phase 2: um 2009 herum. Es kamen Gerüchte auf, dass es den Famo bald als Modell in 1:16 geben wird. Das empfand ich als sehr demotivierend. Außerdem fand ich das Lenkgetriebe als sehr reizvoll zum Nachbauen, was aber in 1:16 für mich nicht in Frage kam. Also habe ich den Zielmaßstab auf 1:10 gewechselt. Ich darf dabei aber nicht zu lange an den Aufwand für das kettenglied denken... Ich habe mich hauptsächlich mit der Analyse des Originals und der Konstruktion des Lenkgetriebes beschäftigt. Dann kam ein Umzug und ein Kind, da war erst mal Pause!
Phase 3: Ab 2014. Ich habe zwischendurch immer mal Recherchiert und am Rechner konstruiert, aber richtig weiter ging es dann im Sommer 2014. In des Lenkgetriebe wieder einzusteigen war mir aber zu sperrig, ich wollte ja motiviert weitermachen. So habe ich mich auf die Vorderreifen gestürzt. Klingt nach nicht viel Arbeit, Näheres dann weiter unten ... . Außerdem wollte ich die Kettenglieder dann nicht mehr selber machen sondern gießen lassen. Dazu brauchte ich auch ein 3D-Modell. So hat sich bis heute eigentlich alles auf die Recherche und Konstruktion am Rechner konzentriert.
Die Phasen im Detail:
Phase 1:
Als Basis dient ein Tamiya 1/35 model (mit Sd.Anh 116) und folgende Bücher und Hefte:
- "Halbkettenfahrzeuge des deutschen Heeres"
- Nuts & Bolts Vol. 12
- Military Machine Famo 18t
- Waffenarsenal Band 36
- Kopie der Dienstvorschrift D671/1 D671/2
- unzählige Bilder aus dem Netz(hier helfen eigentlich nur neue Bilder von Museumsfahrzeugen, alle historischen sind zu ungenau, haben keine Detailsansichten, ...)
Ich möchte die frühe F3 Version bauen.
Auf dem Bild (Link) kann man den Unterschied der Kettenglieder sehen : früh (links) und späte Version (rechts):
http://www.boorad.de/Body/Famo/3d/bb_kette_vergleich.jpg
Weitere Unterschiede sind hauptsächlich an den Kotflügeln und der Front vorhanden.
Ich habe einige Teile in 3D modelliert.
Vorderachse und Felge:
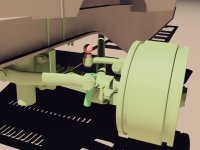
Vorderachse:
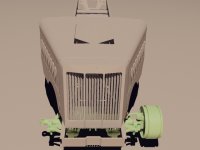
Motorhaube und Grill:
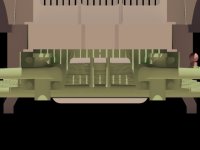
Grill mit Famo-Logo:
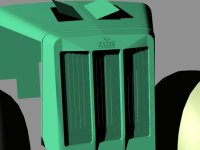
Früher Entwurf des Kettengliedes am Triebrad zur Prüfung der Abmessungen:
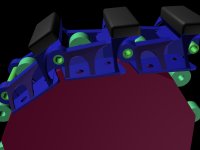
Teile des Prototypes für das Kettenglied. Die Teile sollten einfach herstellbar sein:
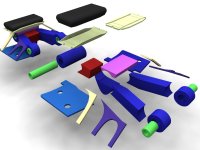
Weiter gehts im nächsten Post...
der Famo, die größte Halbkettenzugmaschine des 2. Weltkrieges, hat mich von dem Moment an fasziniert, als ich vor vielen Jahren den Karton des Tamiya 1/35 Kits auf der Modell Hobby Spiel in Leipzig gesehen habe. Was macht man als junger und unerfahrener Modellbauer? Man sucht sich ein kompliziertes Vorbild und möchte dieses mit ambitionierten Ansprüchen als Modell bauen. Diese Voraussetzungen waren bei mir erfüllt und so beschloss ich, den Famo zu bauen.
Ein Langzeitprojekt ist es jetzt bereits und es wird sicher noch eines für die Zukunft bleiben. Mich stört das aber gar nicht so sehr da die Zeit auch für mich arbeitet - wenn ich nur an die vielen neuen Möglichkeiten denke, die uns Modellbauern nun zur Verfügung stehen...
Bis jetzt gab es grob 3 Phasen des Projektes.
Phase 1: Um 2007 herum. Ich wollte den Famo in 1:16 bauen damit er zu meinem Tamiya Tiger I passt. Ich habe einige 3D-Modelle erstellt. Außerdem habe ich mir eine Fräsmaschine zugelegt(RC-Machines Variante der Rotwerk-Baumarktfräse) Die Kettenglieder wollte ich mit einer selbstgebauten Schleudergussapperatur aus Zamak5 in Silikonform gießen. Den Prototypen dafür habe ich aus Messing gefräst und gelötet.
Phase 2: um 2009 herum. Es kamen Gerüchte auf, dass es den Famo bald als Modell in 1:16 geben wird. Das empfand ich als sehr demotivierend. Außerdem fand ich das Lenkgetriebe als sehr reizvoll zum Nachbauen, was aber in 1:16 für mich nicht in Frage kam. Also habe ich den Zielmaßstab auf 1:10 gewechselt. Ich darf dabei aber nicht zu lange an den Aufwand für das kettenglied denken... Ich habe mich hauptsächlich mit der Analyse des Originals und der Konstruktion des Lenkgetriebes beschäftigt. Dann kam ein Umzug und ein Kind, da war erst mal Pause!
Phase 3: Ab 2014. Ich habe zwischendurch immer mal Recherchiert und am Rechner konstruiert, aber richtig weiter ging es dann im Sommer 2014. In des Lenkgetriebe wieder einzusteigen war mir aber zu sperrig, ich wollte ja motiviert weitermachen. So habe ich mich auf die Vorderreifen gestürzt. Klingt nach nicht viel Arbeit, Näheres dann weiter unten ... . Außerdem wollte ich die Kettenglieder dann nicht mehr selber machen sondern gießen lassen. Dazu brauchte ich auch ein 3D-Modell. So hat sich bis heute eigentlich alles auf die Recherche und Konstruktion am Rechner konzentriert.
Die Phasen im Detail:
Phase 1:
Als Basis dient ein Tamiya 1/35 model (mit Sd.Anh 116) und folgende Bücher und Hefte:
- "Halbkettenfahrzeuge des deutschen Heeres"
- Nuts & Bolts Vol. 12
- Military Machine Famo 18t
- Waffenarsenal Band 36
- Kopie der Dienstvorschrift D671/1 D671/2
- unzählige Bilder aus dem Netz(hier helfen eigentlich nur neue Bilder von Museumsfahrzeugen, alle historischen sind zu ungenau, haben keine Detailsansichten, ...)
Ich möchte die frühe F3 Version bauen.
Auf dem Bild (Link) kann man den Unterschied der Kettenglieder sehen : früh (links) und späte Version (rechts):
http://www.boorad.de/Body/Famo/3d/bb_kette_vergleich.jpg
Weitere Unterschiede sind hauptsächlich an den Kotflügeln und der Front vorhanden.
Ich habe einige Teile in 3D modelliert.
Vorderachse und Felge:
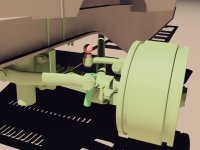
Vorderachse:
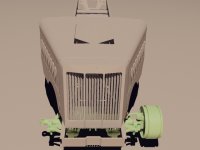
Motorhaube und Grill:
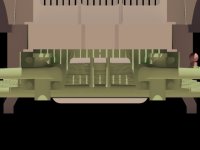
Grill mit Famo-Logo:
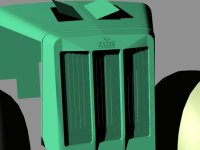
Früher Entwurf des Kettengliedes am Triebrad zur Prüfung der Abmessungen:
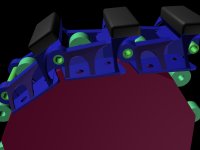
Teile des Prototypes für das Kettenglied. Die Teile sollten einfach herstellbar sein:
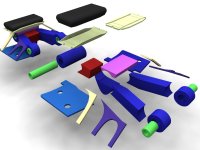
Weiter gehts im nächsten Post...