When I was young I used to go for summer vacations on the Alps in Trentino. There, in a small city called Mezzocorona, there was a wood factory where operated many strange machines. They were like agri tractors but they worked in the opposite way (big wheels ahead) and had arms like wheel loaders with pincers for wood in the place of the bucket. Now I know they were Volvo backloaders, but at the time I watched them with perplexity. They were not good looking, not at all. But they were somehow interesting and always captured my attention when I passed by (usually the first and last day of vacation).
Then I forgot them for some 30 years and, I don't know how or why, they returned into my mind last summer, when I was on vacation in Tuscany. Those days I was lazily designing a wheel loader (CAT 950E) but the process was taking forever. Then, all of a sudden, I decided that my next wheel loader was going to be a Volvo BM LM841. I bought Millimeter paper and I started designing it during the vacation.
This is the machine I am building:
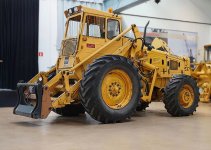
Photo courtesy of Munktell Museum (Eskilstuna). They kindly gave me permission to publish it.
Data about the machine can be found in the museum machine webpage.
Unlike all the other model that I published, this is still a work in progress so I will not publish the finished model picture in the first page nor the GitHub where to download the parts. They will come during the model development.
This is the actual progress:
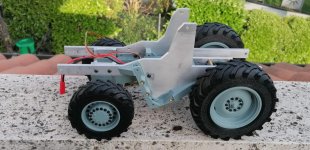
Frame, wheels, axles and transmission are done.
I am proceeding designing the rest of the machine.
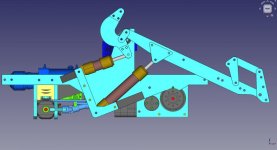
In the following posts I will describe in details the work in progress.
Luca72
Then I forgot them for some 30 years and, I don't know how or why, they returned into my mind last summer, when I was on vacation in Tuscany. Those days I was lazily designing a wheel loader (CAT 950E) but the process was taking forever. Then, all of a sudden, I decided that my next wheel loader was going to be a Volvo BM LM841. I bought Millimeter paper and I started designing it during the vacation.
This is the machine I am building:
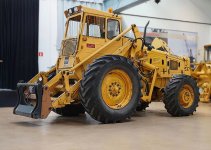
Photo courtesy of Munktell Museum (Eskilstuna). They kindly gave me permission to publish it.
Data about the machine can be found in the museum machine webpage.
Unlike all the other model that I published, this is still a work in progress so I will not publish the finished model picture in the first page nor the GitHub where to download the parts. They will come during the model development.
This is the actual progress:
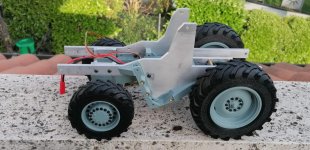
Frame, wheels, axles and transmission are done.
I am proceeding designing the rest of the machine.
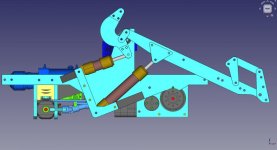
In the following posts I will describe in details the work in progress.
Luca72