- Registriert
- 19.10.2007
- Beiträge
- 2.382
Getriebeölwärmetauscher, Batteriekasten, Radkeile, Druckluftkessel
Hallo Miteinander,
vor dem Weiterbau habe ich erst die Lage der Vorderachsen korrigieren müssen, was auch Änderungen an den Befestigungen/Lagerungen des Fahrerhauses, der Baustellenstoßstange und der Registerkupplung nach sich gezogen hat. Beim Zusammenbau wurden gleich die Bowdenzüge neu verlegt.
Anschließend habe ich aus der Krabbelkiste alles an Kardangelenken zusammen gesucht was ich finden konnte und mir vier Kardanwellen mit Längenausgleich zusammengebaut. Zu große Bohrungen in den Gelenken habe ich mit Messingrohreinsätzen ausgeglichen. Die Knickwinkel habe ich sehr gering halten können.
Sichtbare Messing- Sechskantwellen am fertigen TGA werde ich noch in einem Rohr verstecken.
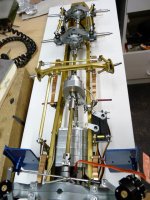
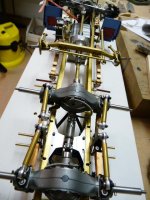
Weiter ist es mit den Anbauteilen links hinter dem Fahrerhaus am Rahmen gegangen.
Zuerst habe ich mir einen Halter aus Messing gebaut, an dem alles verschraubt wird. Der Halter selbst ist an zwei fest am Rahmen verschraubten M2- Schrauben befestigt. Auch hier ist, wie bei der gegenüberliegenden Staukasten/Servohalterung, beim Entfernen kein Gegenhalten der unzugänglich im Rahmeninneren liegenden Schraubenköpfe nötig.
Ich versuche so zu bauen, dass alles leicht, schnell und Baugruppenweise demontierbar ist. Das ist die Konsequenz aus den Erfahrungen mit der kurzen SLZM.
Beim Original sitzt alles näher am Rahmen. Wegen der Anlenkstange zur zweiten Vorderachse musste ich hier trotz Manipulationen an den Anbauteilen einen Kompromiss eingehen und die Baugruppen etwas weiter nach außen verlegen.
Auf dem nächsten Foto ist bereits der Metallkorb des Getriebeölwärmetauschers, den ich aus 0,5mm Ms zusammengelötet habe, angeschraubt. Für was der gut ist, keine Ahnung, vielleicht als Schutz? Im hinteren Bereich habe ich ihn so abgeändert, dass die Lenkstangenbewegung zur zweiten Vorderachse nicht behindert wird. Die Halterung schaut schief aus, das kommt aber von der Rahmenschweifung/Verjüngung an dieser Stelle.
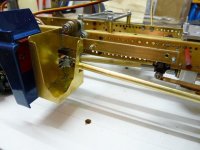
Dann habe ich den Getriebeölwärmetauscher nach Fotos aus PS nachgebaut.
Die leicht wellige/streifenartige Struktur im Frontbereich habe ich bekommen, indem ich 0,5mm PS- Streifen ausgeschnitten und die Längskanten gebrochen habe. Die Streifen wurden dann aufeinander geklebt.
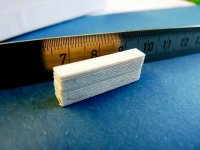
Die Kanten habe ich bewusst nicht verspachtelt und sauber verschliffen, weil man diese bzw. die Schweißnähte auch beim Original sieht. Den Wärmetauscher habe ich dann auf Abstand im Metallkorb aufgehängt.
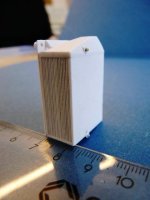
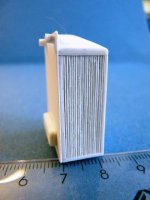
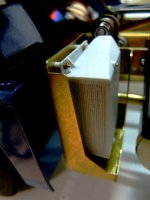
Der Batteriekasten stammt vom ScaleART- Schwerlastturm des kurzen TGA. Der Deckel wurde mit Hilfe von zwei links und rechts eingesetzten Ms- Drähten aufklappbar umgebaut. Als ich den Knebelschalter und ein Vorhängeschloss auf einem Foto entdeckt habe, war’s mal wieder so weit: ich hatte Lust auf Details und Platz im Batteriekasten war da.
Knebelschalter (vom Fahrer stecken gelassen
), Kastenverschlüsse und Bügelschloss.
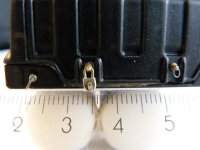
Als Vorbild für die beiden Batterien hat ein 12V- Banner Buffalo Bull mit 180Ah herhalten müssen. Die Tragegriffe lassen sich ein- und aus schieben.
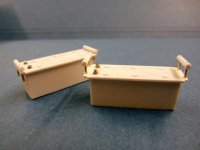
Der Batteriehalterahmen ist wie die Batterien aus PS entstanden. In den Mittelsteg sind zwei M1,2 –Ms- Gewindestangen geschraubt und geklebt, an denen die Querprofile für die Befestigung der beiden Batterien verschraubt sind.
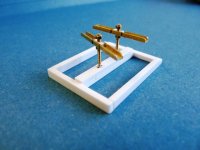
Hinter den Knebelschalter habe ich noch einen „Schaltkasten“ gebaut. Zuletzt habe ich die Verkabelung mit den Polklemmen nachgebaut. Der Knebelschalter ist auch zu erkennen.
Ob beim Original auch alles so aussieht weis ich nicht, ich habe meiner Kreativität freien Lauf gelassen.
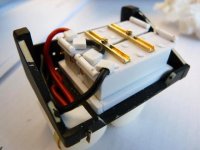
Gleich geht’s weiter…
Hallo Miteinander,
vor dem Weiterbau habe ich erst die Lage der Vorderachsen korrigieren müssen, was auch Änderungen an den Befestigungen/Lagerungen des Fahrerhauses, der Baustellenstoßstange und der Registerkupplung nach sich gezogen hat. Beim Zusammenbau wurden gleich die Bowdenzüge neu verlegt.
Anschließend habe ich aus der Krabbelkiste alles an Kardangelenken zusammen gesucht was ich finden konnte und mir vier Kardanwellen mit Längenausgleich zusammengebaut. Zu große Bohrungen in den Gelenken habe ich mit Messingrohreinsätzen ausgeglichen. Die Knickwinkel habe ich sehr gering halten können.
Sichtbare Messing- Sechskantwellen am fertigen TGA werde ich noch in einem Rohr verstecken.
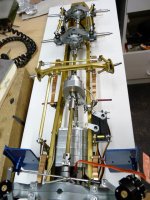
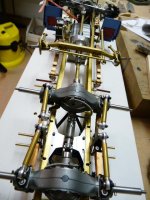
Weiter ist es mit den Anbauteilen links hinter dem Fahrerhaus am Rahmen gegangen.
Zuerst habe ich mir einen Halter aus Messing gebaut, an dem alles verschraubt wird. Der Halter selbst ist an zwei fest am Rahmen verschraubten M2- Schrauben befestigt. Auch hier ist, wie bei der gegenüberliegenden Staukasten/Servohalterung, beim Entfernen kein Gegenhalten der unzugänglich im Rahmeninneren liegenden Schraubenköpfe nötig.
Ich versuche so zu bauen, dass alles leicht, schnell und Baugruppenweise demontierbar ist. Das ist die Konsequenz aus den Erfahrungen mit der kurzen SLZM.
Beim Original sitzt alles näher am Rahmen. Wegen der Anlenkstange zur zweiten Vorderachse musste ich hier trotz Manipulationen an den Anbauteilen einen Kompromiss eingehen und die Baugruppen etwas weiter nach außen verlegen.
Auf dem nächsten Foto ist bereits der Metallkorb des Getriebeölwärmetauschers, den ich aus 0,5mm Ms zusammengelötet habe, angeschraubt. Für was der gut ist, keine Ahnung, vielleicht als Schutz? Im hinteren Bereich habe ich ihn so abgeändert, dass die Lenkstangenbewegung zur zweiten Vorderachse nicht behindert wird. Die Halterung schaut schief aus, das kommt aber von der Rahmenschweifung/Verjüngung an dieser Stelle.
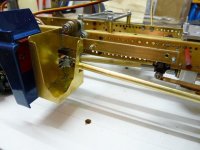
Dann habe ich den Getriebeölwärmetauscher nach Fotos aus PS nachgebaut.
Die leicht wellige/streifenartige Struktur im Frontbereich habe ich bekommen, indem ich 0,5mm PS- Streifen ausgeschnitten und die Längskanten gebrochen habe. Die Streifen wurden dann aufeinander geklebt.
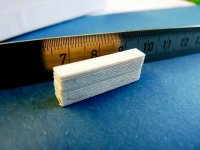
Die Kanten habe ich bewusst nicht verspachtelt und sauber verschliffen, weil man diese bzw. die Schweißnähte auch beim Original sieht. Den Wärmetauscher habe ich dann auf Abstand im Metallkorb aufgehängt.
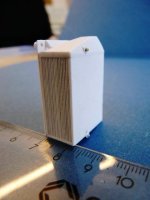
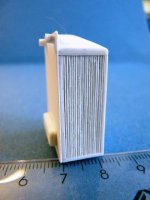
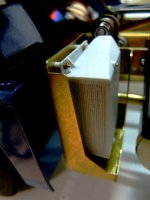
Der Batteriekasten stammt vom ScaleART- Schwerlastturm des kurzen TGA. Der Deckel wurde mit Hilfe von zwei links und rechts eingesetzten Ms- Drähten aufklappbar umgebaut. Als ich den Knebelschalter und ein Vorhängeschloss auf einem Foto entdeckt habe, war’s mal wieder so weit: ich hatte Lust auf Details und Platz im Batteriekasten war da.
Knebelschalter (vom Fahrer stecken gelassen

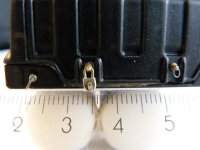
Als Vorbild für die beiden Batterien hat ein 12V- Banner Buffalo Bull mit 180Ah herhalten müssen. Die Tragegriffe lassen sich ein- und aus schieben.
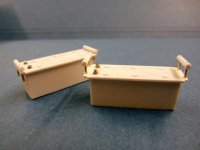
Der Batteriehalterahmen ist wie die Batterien aus PS entstanden. In den Mittelsteg sind zwei M1,2 –Ms- Gewindestangen geschraubt und geklebt, an denen die Querprofile für die Befestigung der beiden Batterien verschraubt sind.
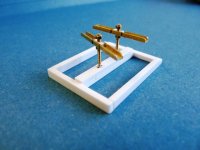
Hinter den Knebelschalter habe ich noch einen „Schaltkasten“ gebaut. Zuletzt habe ich die Verkabelung mit den Polklemmen nachgebaut. Der Knebelschalter ist auch zu erkennen.
Ob beim Original auch alles so aussieht weis ich nicht, ich habe meiner Kreativität freien Lauf gelassen.
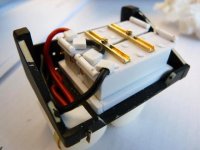
Gleich geht’s weiter…
Zuletzt bearbeitet: