mga_1500
Active member
- Registriert
- 19.02.2014
- Beiträge
- 212
Hallo zusammen 
Ich finde es ist mal wieder Zeit, (m)ein neues Projekt vorzustellen.
Um ehrlich zu sein, arbeite ich schon eine Weile daran. Auch bin ich schon fleißig am Protokollieren, dass auch ja nichts vergessen wird.
(Ist nun vielleicht ein bisschen langatmig für den Anfang. Ich weiß ja, dass viele von euch lieber Bilder schauen als lesen. Es gibt auch noch jede Menge Bilder. Versprochen! Wenn es euch zu viel Text ist, schreibt es mir einfach!!!)
Nachdem der Tieflader einen nahezu fertigen Stand erreicht hatte, waren Überlegungen notwendig, was denn als Nachfolgeprojekt eventuell in Frage kommen könnte.
Die vielen Beiträge in unserem Forum waren so vielschichtig, dass mir die Wahl zu Beginn recht schwer viel. Es war für mich allerdings schon relativ schnell klar, dass es wieder etwas werden sollte, das noch nicht da gewesen ist. Ich wollte auch unbedingt einen LKW erstellen und nicht noch einmal ein Anhängsel, welches zu meinem WEDICO Conventional passen sollte / könnte.
Die Art und Weise des Fahrzeug-Aufbaus, in Bezug auf das zu verwendete Material, war ebenfalls schon sehr schnell klar gewesen. Es sollte ein Projekt werden, welches mit / aus Blech gefertigt werden kann. Die Materialien Kupfer, Messing, und Aluminium sollten dabei Anwendung finden. Nach einer ca. vierwöchigen Zeit der Recherche, in der ich immer wieder, wenn es die Zeit erlaubte, viele Bilder im WWW suchte und fand, war dann der Entschluss gefasst, in einer bestimmten Richtung weiterzuforschen!
Es sollte ein L10000 aus dem Hause Mercedes werden.
Da es bei diesem LKW nur einige Bilder von richtigen / echten alten Fahrzeugen „im Netz“ gab, hoffte ich für mich auf ein paar bessere „Rahmenbedingungen“, den Kollegen gegenüber, welche sich schon an diesem Fahrzeug versuchten! Die im WWW erhältlichen Informationen ließen nämlich den Schluss zu, dass es von diesem Fahrzeug keine Zeichnungen, Rahmenstrukturen oder Maßangaben gab.
Dieser Umstand machte das Ganze Projekt natürlich nicht einfacher – aber umso reizvoller!!!
Beim darüber nachdenken, wie sich solch ein LKW machen lässt, kam ich an den komischsten Gedanken vorbei. Diese waren aber nur zu Beginn „komisch“. Am 11. August 2015 hatte ich dann eine Email an unsere Damen im Daimler Archiv geschickt, in der ich anfragte, ob es denn zu dem L10000 Archivmaterial, egal in welcher Ausprägung, gibt! Da das Archiv zu diesem Zeitpunkt mit Umzugs-Aktivitäten beschäftigt war, rechnete ich mit einer etwas längeren „Antworts-Zeit“!!! Umso mehr war ich sehr überrascht schon kurz nach der Mittagspause eine Antwort mit einer PDF als Anhang zu erhalten. Somit war das Projekt gestartet!!!
Es stellte sich allerdings sehr schnell heraus, dass das abgebildete Fahrzeug in dieser PDF nicht für „meinen“ L10000 passte. Allerdings habe ich auch keine Ahnung, zu welchem Lastwagen dieses passte!!!
Weiterhin konnte ich vom Daimler-Archiv dann auch noch eine Vielzahl von Bildern und den damaligen „Verkaufs-Prospekt“ in Datenform bekommen. Dies waren allerdings Unterlagen, in denen es keine genauen Maßangaben gab. Lediglich der Prospekt beinhaltete elementare Maße wie Gesamtlänge, Breite, Höhe, die Radstände und Spurweiten und die Angaben zur Pritsche / Ladefläche. Ebenfalls waren die Leistungs-, Verbrauchs- und Geschwindigkeitsangeben enthalten, welche aber für mich nicht unbedingt wichtig waren.
Mit diesen Unterlagen und den Informationen aus dem WWW formte sich langsam aber sicher ein „Bild“ in meinem Kopf. Im Verlaufe der weiteren Überlegungen und Recherchen kam irgendwann DER entscheidende Hinweis! Der Rahmen des L10000 ist in vielen Bereichen identisch zum Rahmen des O10000, welches der Omnibus aus der damaligen Zeit war!
Mit diesem Wissen wurde dann noch einmal im Daimler-Archiv nachgefragt. Von dort kamen dann weitere PDF-Dokumente, in denen man sehr detailliert die Rahmenstruktur mit den jeweiligen Verstrebungen und Quertraversen erkennen konnte.
Mit den nun vorhandenen Informationen (Radstände und Bildmaterial von seitlicher Darstellung) konnten mittels einfacher „Dreisatzrechnungen“ zumindest mal die groben Maße der Proportionen ermittelt werden. Es kam aber noch besser!!!
Einer der sehr raren noch vorhandenen Exponate ist der im Mercedes-Museum stehende O10000 der „Reichspost“ (mobiles Postamt!). Durch die positive Resonanz seitens Daimler-Archiv war ich „ermutigt“ ähnliches im Mercedes-Museum zu erfragen!!!
Kurzerhand wurde an die „Classic-Mailbox“ eine Mail mit dem Titel „O10000 - Rollende Poststation und L6500 – Pritschenwagen“ formuliert und abgeschickt.
Ich erspare euch nun dieses.
Um ehrlich zu sein, ich hatte schon ein sehr komisches Gefühl in der Magengegend, als ich nach der Formulierung der Email auf den „SENDEN-Knopf“ gedrückt hatte. Nun begann also die Lange Zeit des Wartens auf Antwort!
Mitnichten!!! Bereits schon am gleichen Tag erhielt ich vom zuständigen Ansprechpartner im Museum folgende Antwort: (Originaltext!)
Hallo Herr XXXXX,
unser Kundencenter hat mir Ihre Anfrage weitergeleitet.
Ich bin hier im Haus für die FZG in der Ausstellung verantwortlich.
Sehr gerne können Sie bei uns im Haus Maße an unserem Postbus und am L6500 nehmen. Auch Detailbilder sind selbstverständlich kein Problem.
Die FZG stehen beide in Collection 2 "Galerie der Lasten".
Am besten wäre es, wenn Sie an einem Montag kommen könnten. Da ist das Museum geschlossen und Sie können in aller Ruhe messen & Photographien.
Bitte geben Sie einfach Bescheid, wann Sie kommen möchten.
Herzliche Grüße,
Ich muss gestehen, dass ich leicht feuchte Augen bekam, als ich dieses Email gelesen hatte. Das war DER Durchbruch für mich und es stand nun fest, dass das „Projekt L10000“ definitiv geboren war!!!
Ich machte mir danach meine Gedanken, wie ich sicherstellen konnte, dass auch alles, was für die Konstruktion / den Nachbau notwendig war, auch gemessen und aufgeschrieben werden konnte. Die Beste Lösung für mich war, alles Wichtige zu skizzieren. So begann also die lange Zeit, in der ich anhand der vielen zur Verfügung gestellten Bildern meine persönlichen Hand-Skizzen erstellte. Diese sollten dazu dienen, ein besseres Verständnis über die damalige Bauweise zu bekommen und dass alle notwendigen Maße notiert werden konnten. Hier ein kleiner Auszug der von mir angefertigten Handskizzen:
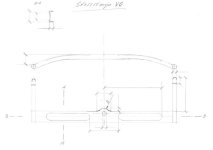
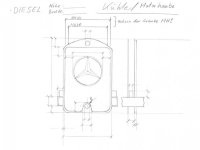
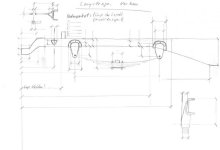
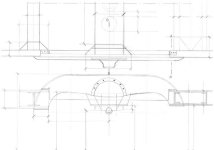
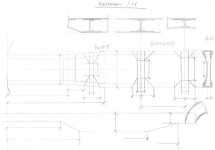

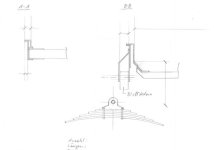
Dieses „Unterfangen“ zog sich dann bis ca. Mitte / Ende Oktober 2015 hin. In den Mittagspausen, während meine Kolleginnen und Kollegen sich die Bäuche füllten, war ich damit beschäftigt, die vorhandenen Unterlagen zu vermessen, zu vergleichen und meine Blätter mit Bleistiftstrichen zu füllen. Nachdem dann alle relevanten Bereiche mit Skizzen versehen waren, konnte ein Termin im Museum ausgemacht werden, damit die Fahrzeuge vermessen werden konnten.
Am 2. November 2015 war es dann soweit. Ein Montag-Termin war gefunden und ich marschierte ins Museum, um für „Meinen L10000“ die ach so wichtigen Maße zu nehmen!
Nachdem der Museumsverantwortliche und ich uns am Lieferanteneingang trafen, ging es direkt an die „Objekte meiner Begierde!“ Es war schon ein sehr erhebendes Gefühl, diese Möglichkeiten eigeräumt bekommen zu haben!
Mein Equipment umfasste natürlich meine Skizzen, mehrere Meterstäbe, einen Fotoapparat und die ganz wichtigen Handschuhe, um keine Kratzer zu hinterlassen. In den folgenden 6 Stunden wurden am O10000 und am L6500 Pritschenwagen von vorne bis hinten und meist unter den Fahrzeugen liegend, die wichtigsten Maße genommen und notiert!!!
Da nun die wichtigsten Eckdaten / Maße vorhanden waren musste ich mir noch zum „Maßstab meines Projektes“ die notwendigen Gedanken machen. Wichtig war mir hierbei, dass es so gut wie möglich „scalig“ aussehen sollte. Der Maßstab 1:16, welchen ich bisher als mein „homefield“ ansah, schied für mich aus, da eine Schraubengröße kleiner als M2, für mich nicht in Frage kam! Blieben nur noch 1:10 oder doch gleich 1:8!
Die Wahl fiel schließlich auf 1:8, da dies für die Antriebsachsen, welche ich mit meinen Möglichkeiten und Mitteln nicht selbst herstellen kann, im Zubehörhandel gängiger sind! Das Umrechnen der Maße auf diesen Maßstab ist zwar etwas aufwändiger, aber mit Taschenrechner und Computer ist das ja heutzutage kein Problem!
Die zu verwendenden Materialien werden weitestgehend, wie schon einmal erwähnt Bleche und Profile aus Metall sein. Aluminium, Messing und Kupfer kommen hier bevorzugt zum Einsatz. Aluminium an den Bauteilen, wo die Befestigung mittels Schrauben erfolgen soll / kann. Messing und Kupfer sollten in den Bereichen verwendet werden, wo ab und an auch mal weich-gelötet werden muss.
Die ersten „CAD-Pinselstriche“ waren bald gemacht und sogleich wurde auch festgestellt, dass die Konstruktion wohl auch nicht unbedingt immer ganz einfach sein / werden würde!!!
Nun, soviel mal für heute!
Ist vielleicht doch etwas viel Text für den Anfang. Wer nicht so viel lesen will, der kann ja mal mit den Bildern vorlieb nehmen!!!
Trotz allem "Viel Spaß" beim mitlesen und zuschauen und natürlich auch beim kommentieren ...
Bis bald.

Ich finde es ist mal wieder Zeit, (m)ein neues Projekt vorzustellen.

Um ehrlich zu sein, arbeite ich schon eine Weile daran. Auch bin ich schon fleißig am Protokollieren, dass auch ja nichts vergessen wird.
(Ist nun vielleicht ein bisschen langatmig für den Anfang. Ich weiß ja, dass viele von euch lieber Bilder schauen als lesen. Es gibt auch noch jede Menge Bilder. Versprochen! Wenn es euch zu viel Text ist, schreibt es mir einfach!!!)
Nachdem der Tieflader einen nahezu fertigen Stand erreicht hatte, waren Überlegungen notwendig, was denn als Nachfolgeprojekt eventuell in Frage kommen könnte.
Die vielen Beiträge in unserem Forum waren so vielschichtig, dass mir die Wahl zu Beginn recht schwer viel. Es war für mich allerdings schon relativ schnell klar, dass es wieder etwas werden sollte, das noch nicht da gewesen ist. Ich wollte auch unbedingt einen LKW erstellen und nicht noch einmal ein Anhängsel, welches zu meinem WEDICO Conventional passen sollte / könnte.
Die Art und Weise des Fahrzeug-Aufbaus, in Bezug auf das zu verwendete Material, war ebenfalls schon sehr schnell klar gewesen. Es sollte ein Projekt werden, welches mit / aus Blech gefertigt werden kann. Die Materialien Kupfer, Messing, und Aluminium sollten dabei Anwendung finden. Nach einer ca. vierwöchigen Zeit der Recherche, in der ich immer wieder, wenn es die Zeit erlaubte, viele Bilder im WWW suchte und fand, war dann der Entschluss gefasst, in einer bestimmten Richtung weiterzuforschen!
Es sollte ein L10000 aus dem Hause Mercedes werden.
Da es bei diesem LKW nur einige Bilder von richtigen / echten alten Fahrzeugen „im Netz“ gab, hoffte ich für mich auf ein paar bessere „Rahmenbedingungen“, den Kollegen gegenüber, welche sich schon an diesem Fahrzeug versuchten! Die im WWW erhältlichen Informationen ließen nämlich den Schluss zu, dass es von diesem Fahrzeug keine Zeichnungen, Rahmenstrukturen oder Maßangaben gab.
Dieser Umstand machte das Ganze Projekt natürlich nicht einfacher – aber umso reizvoller!!!
Beim darüber nachdenken, wie sich solch ein LKW machen lässt, kam ich an den komischsten Gedanken vorbei. Diese waren aber nur zu Beginn „komisch“. Am 11. August 2015 hatte ich dann eine Email an unsere Damen im Daimler Archiv geschickt, in der ich anfragte, ob es denn zu dem L10000 Archivmaterial, egal in welcher Ausprägung, gibt! Da das Archiv zu diesem Zeitpunkt mit Umzugs-Aktivitäten beschäftigt war, rechnete ich mit einer etwas längeren „Antworts-Zeit“!!! Umso mehr war ich sehr überrascht schon kurz nach der Mittagspause eine Antwort mit einer PDF als Anhang zu erhalten. Somit war das Projekt gestartet!!!
Es stellte sich allerdings sehr schnell heraus, dass das abgebildete Fahrzeug in dieser PDF nicht für „meinen“ L10000 passte. Allerdings habe ich auch keine Ahnung, zu welchem Lastwagen dieses passte!!!
Weiterhin konnte ich vom Daimler-Archiv dann auch noch eine Vielzahl von Bildern und den damaligen „Verkaufs-Prospekt“ in Datenform bekommen. Dies waren allerdings Unterlagen, in denen es keine genauen Maßangaben gab. Lediglich der Prospekt beinhaltete elementare Maße wie Gesamtlänge, Breite, Höhe, die Radstände und Spurweiten und die Angaben zur Pritsche / Ladefläche. Ebenfalls waren die Leistungs-, Verbrauchs- und Geschwindigkeitsangeben enthalten, welche aber für mich nicht unbedingt wichtig waren.
Mit diesen Unterlagen und den Informationen aus dem WWW formte sich langsam aber sicher ein „Bild“ in meinem Kopf. Im Verlaufe der weiteren Überlegungen und Recherchen kam irgendwann DER entscheidende Hinweis! Der Rahmen des L10000 ist in vielen Bereichen identisch zum Rahmen des O10000, welches der Omnibus aus der damaligen Zeit war!
Mit diesem Wissen wurde dann noch einmal im Daimler-Archiv nachgefragt. Von dort kamen dann weitere PDF-Dokumente, in denen man sehr detailliert die Rahmenstruktur mit den jeweiligen Verstrebungen und Quertraversen erkennen konnte.
Mit den nun vorhandenen Informationen (Radstände und Bildmaterial von seitlicher Darstellung) konnten mittels einfacher „Dreisatzrechnungen“ zumindest mal die groben Maße der Proportionen ermittelt werden. Es kam aber noch besser!!!
Einer der sehr raren noch vorhandenen Exponate ist der im Mercedes-Museum stehende O10000 der „Reichspost“ (mobiles Postamt!). Durch die positive Resonanz seitens Daimler-Archiv war ich „ermutigt“ ähnliches im Mercedes-Museum zu erfragen!!!
Kurzerhand wurde an die „Classic-Mailbox“ eine Mail mit dem Titel „O10000 - Rollende Poststation und L6500 – Pritschenwagen“ formuliert und abgeschickt.
Ich erspare euch nun dieses.
Um ehrlich zu sein, ich hatte schon ein sehr komisches Gefühl in der Magengegend, als ich nach der Formulierung der Email auf den „SENDEN-Knopf“ gedrückt hatte. Nun begann also die Lange Zeit des Wartens auf Antwort!
Mitnichten!!! Bereits schon am gleichen Tag erhielt ich vom zuständigen Ansprechpartner im Museum folgende Antwort: (Originaltext!)
Hallo Herr XXXXX,
unser Kundencenter hat mir Ihre Anfrage weitergeleitet.
Ich bin hier im Haus für die FZG in der Ausstellung verantwortlich.
Sehr gerne können Sie bei uns im Haus Maße an unserem Postbus und am L6500 nehmen. Auch Detailbilder sind selbstverständlich kein Problem.
Die FZG stehen beide in Collection 2 "Galerie der Lasten".
Am besten wäre es, wenn Sie an einem Montag kommen könnten. Da ist das Museum geschlossen und Sie können in aller Ruhe messen & Photographien.
Bitte geben Sie einfach Bescheid, wann Sie kommen möchten.
Herzliche Grüße,
Ich muss gestehen, dass ich leicht feuchte Augen bekam, als ich dieses Email gelesen hatte. Das war DER Durchbruch für mich und es stand nun fest, dass das „Projekt L10000“ definitiv geboren war!!!
Ich machte mir danach meine Gedanken, wie ich sicherstellen konnte, dass auch alles, was für die Konstruktion / den Nachbau notwendig war, auch gemessen und aufgeschrieben werden konnte. Die Beste Lösung für mich war, alles Wichtige zu skizzieren. So begann also die lange Zeit, in der ich anhand der vielen zur Verfügung gestellten Bildern meine persönlichen Hand-Skizzen erstellte. Diese sollten dazu dienen, ein besseres Verständnis über die damalige Bauweise zu bekommen und dass alle notwendigen Maße notiert werden konnten. Hier ein kleiner Auszug der von mir angefertigten Handskizzen:
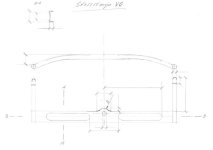
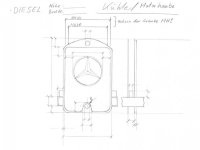
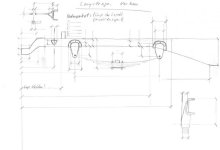
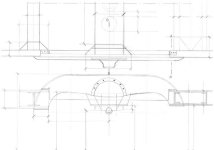
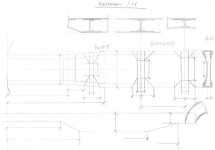

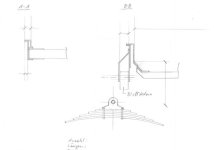
Dieses „Unterfangen“ zog sich dann bis ca. Mitte / Ende Oktober 2015 hin. In den Mittagspausen, während meine Kolleginnen und Kollegen sich die Bäuche füllten, war ich damit beschäftigt, die vorhandenen Unterlagen zu vermessen, zu vergleichen und meine Blätter mit Bleistiftstrichen zu füllen. Nachdem dann alle relevanten Bereiche mit Skizzen versehen waren, konnte ein Termin im Museum ausgemacht werden, damit die Fahrzeuge vermessen werden konnten.
Am 2. November 2015 war es dann soweit. Ein Montag-Termin war gefunden und ich marschierte ins Museum, um für „Meinen L10000“ die ach so wichtigen Maße zu nehmen!
Nachdem der Museumsverantwortliche und ich uns am Lieferanteneingang trafen, ging es direkt an die „Objekte meiner Begierde!“ Es war schon ein sehr erhebendes Gefühl, diese Möglichkeiten eigeräumt bekommen zu haben!
Mein Equipment umfasste natürlich meine Skizzen, mehrere Meterstäbe, einen Fotoapparat und die ganz wichtigen Handschuhe, um keine Kratzer zu hinterlassen. In den folgenden 6 Stunden wurden am O10000 und am L6500 Pritschenwagen von vorne bis hinten und meist unter den Fahrzeugen liegend, die wichtigsten Maße genommen und notiert!!!
Da nun die wichtigsten Eckdaten / Maße vorhanden waren musste ich mir noch zum „Maßstab meines Projektes“ die notwendigen Gedanken machen. Wichtig war mir hierbei, dass es so gut wie möglich „scalig“ aussehen sollte. Der Maßstab 1:16, welchen ich bisher als mein „homefield“ ansah, schied für mich aus, da eine Schraubengröße kleiner als M2, für mich nicht in Frage kam! Blieben nur noch 1:10 oder doch gleich 1:8!
Die Wahl fiel schließlich auf 1:8, da dies für die Antriebsachsen, welche ich mit meinen Möglichkeiten und Mitteln nicht selbst herstellen kann, im Zubehörhandel gängiger sind! Das Umrechnen der Maße auf diesen Maßstab ist zwar etwas aufwändiger, aber mit Taschenrechner und Computer ist das ja heutzutage kein Problem!
Die zu verwendenden Materialien werden weitestgehend, wie schon einmal erwähnt Bleche und Profile aus Metall sein. Aluminium, Messing und Kupfer kommen hier bevorzugt zum Einsatz. Aluminium an den Bauteilen, wo die Befestigung mittels Schrauben erfolgen soll / kann. Messing und Kupfer sollten in den Bereichen verwendet werden, wo ab und an auch mal weich-gelötet werden muss.
Die ersten „CAD-Pinselstriche“ waren bald gemacht und sogleich wurde auch festgestellt, dass die Konstruktion wohl auch nicht unbedingt immer ganz einfach sein / werden würde!!!
Nun, soviel mal für heute!
Ist vielleicht doch etwas viel Text für den Anfang. Wer nicht so viel lesen will, der kann ja mal mit den Bildern vorlieb nehmen!!!
Trotz allem "Viel Spaß" beim mitlesen und zuschauen und natürlich auch beim kommentieren ...
Bis bald.