mga_1500
Active member
- Registriert
- 19.02.2014
- Beiträge
- 212
Hallo und Guten Abend an alle. 
Ich habe noch ein bisschen weiter scheffeln können.
cool
Aber seht selbst.
Nachdem der Rahmen fertig war, konnte mit dem Füllblech und der Befestigungselemente weiter gemacht werden. Zuerst wurde ein 2mm Messingblech passend gesägt und gefeilt. Im Nachgang dann eingelötet. Damit dann später die Abschlussplatine mit der Außenform / Kontur flächig aufgelötet werden kann, musste der erste Teil im Bereich der Lötnaht eingeebnet werden.
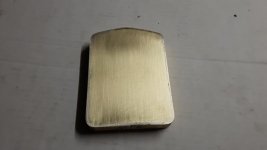
Für die Befestigungselemente zum Längsträger hin mussten im unteren Bereich jeweils ein 7x7mm Vierkantloch und 2 runde Löcher gebohrt werden. Hier sieht man schon ein Vierkantstück bereits verschraubt.
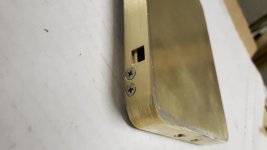
So sieht das dann von Innen aus.
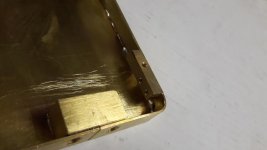
Hier nun der auf der anderen Seite bereits fertiggestellte Zusammenbau. Zuerst von Innen, im Weiteren dann von außen gesehen, beidseitig fertig gestellt.
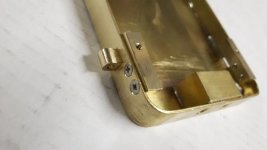
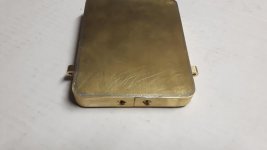
In diesem Status wurden dann diverse andere, noch fehlende Tätigkeiten gemacht. Als erstes wurde an der Motorhaube (Mittelteil) ein kleines Befestigungsblech angelötet. An diesem wird Motorhaube und Kühler fest miteinander verschraubt.
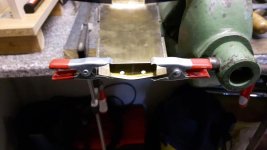
Es hatte sich nach dem Zusammenschrauben leider gezeigt, dass die seitlichen oberen klappbaren Teile keinen sauberen Übergang zum Kühler hatten. Nach dem Anpassen sieht das nun so aus. Das ist für mich ein akzeptabler Zustand.
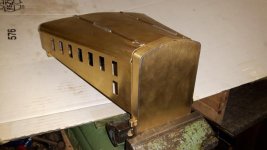
Ferner wurden die Löcher in den Rahmen-Teilen angerissen (In der Gewindeplatte im Bereich der Lampenbefestigung) und gebohrt, damit der Kühler dann auch mal auf dem Rahmen verschraubt werden kann.
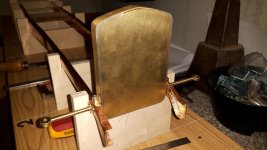
Im folgenden Bild dann der zusammengeschraubte Verbund Kühler / Motorhaube / Trennwand nur mal lose auf die Rahmenprofile positioniert.
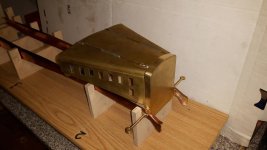
Für die finale Optik des Kühlers ging es mit einem weiteren Blech weiter. Dieses soll dann auf den schon grob fertiggestellten Kühler aufgelötet werden. Zuerst war es aufzuzeichnen und auszusägen. Die gebohrten Löcher sollen später die Rundungen ergeben. Die meisten waren auch gut positioniert. Die äußeren Sägeschnitte wurden mit der Stichsäge gemacht.
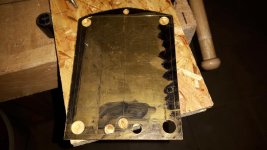
Eine halbe Stunde und ein Laubsägen-Blatt später sah das dann so aus.
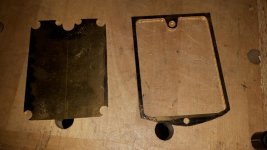
Nach dem Fein-bearbeiten der inneren Kontur (Sägeschnittlinie) des rechten Teiles wurde es auf den Kühler aufgelötet. Die Bearbeitung der äußeren Kontur erfolgte erst nach dem Anbringen. Hier noch vor der Außen-Bearbeitung, nur der aufgelötete „schmale Rahmen“ wurde im Bereich der Lötnaht bearbeitet.
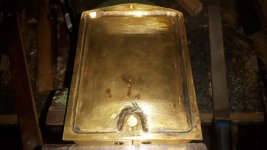
Der vorerst mal fertige Kühler, auf die Längsträger geschraubt, sieht so aus. Für das DIESEL-Logo mit Stern muss ich mir noch etwas einfallen lassen. Diese Teile werden dann aber auch erst nach dem Lackieren angebracht. Tendenziell werden diese / wird das dann schraubbar werden. Ein Loch im Kühler ist dann schnell gebohrt.
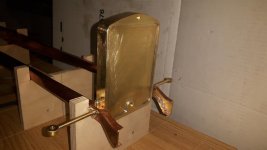
So meine Lieben, das war es schon wieder für heute. Viel Spaß beim lesen und kommentieren.
Bis bald mal wieder.

Ich habe noch ein bisschen weiter scheffeln können.

Aber seht selbst.
Nachdem der Rahmen fertig war, konnte mit dem Füllblech und der Befestigungselemente weiter gemacht werden. Zuerst wurde ein 2mm Messingblech passend gesägt und gefeilt. Im Nachgang dann eingelötet. Damit dann später die Abschlussplatine mit der Außenform / Kontur flächig aufgelötet werden kann, musste der erste Teil im Bereich der Lötnaht eingeebnet werden.
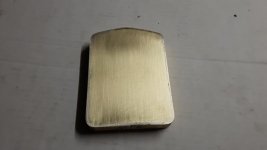
Für die Befestigungselemente zum Längsträger hin mussten im unteren Bereich jeweils ein 7x7mm Vierkantloch und 2 runde Löcher gebohrt werden. Hier sieht man schon ein Vierkantstück bereits verschraubt.
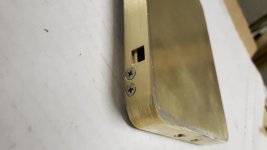
So sieht das dann von Innen aus.
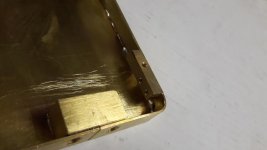
Hier nun der auf der anderen Seite bereits fertiggestellte Zusammenbau. Zuerst von Innen, im Weiteren dann von außen gesehen, beidseitig fertig gestellt.
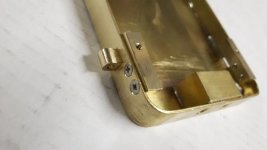
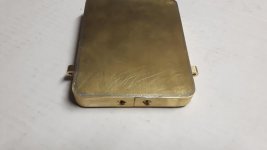
In diesem Status wurden dann diverse andere, noch fehlende Tätigkeiten gemacht. Als erstes wurde an der Motorhaube (Mittelteil) ein kleines Befestigungsblech angelötet. An diesem wird Motorhaube und Kühler fest miteinander verschraubt.
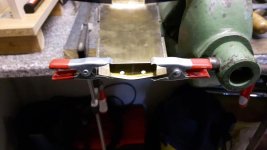
Es hatte sich nach dem Zusammenschrauben leider gezeigt, dass die seitlichen oberen klappbaren Teile keinen sauberen Übergang zum Kühler hatten. Nach dem Anpassen sieht das nun so aus. Das ist für mich ein akzeptabler Zustand.
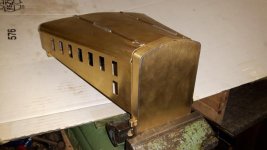
Ferner wurden die Löcher in den Rahmen-Teilen angerissen (In der Gewindeplatte im Bereich der Lampenbefestigung) und gebohrt, damit der Kühler dann auch mal auf dem Rahmen verschraubt werden kann.
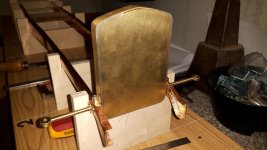
Im folgenden Bild dann der zusammengeschraubte Verbund Kühler / Motorhaube / Trennwand nur mal lose auf die Rahmenprofile positioniert.
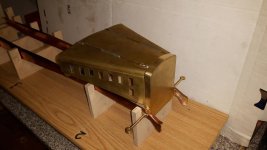
Für die finale Optik des Kühlers ging es mit einem weiteren Blech weiter. Dieses soll dann auf den schon grob fertiggestellten Kühler aufgelötet werden. Zuerst war es aufzuzeichnen und auszusägen. Die gebohrten Löcher sollen später die Rundungen ergeben. Die meisten waren auch gut positioniert. Die äußeren Sägeschnitte wurden mit der Stichsäge gemacht.
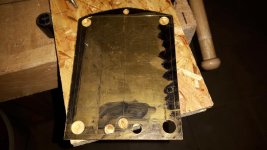
Eine halbe Stunde und ein Laubsägen-Blatt später sah das dann so aus.
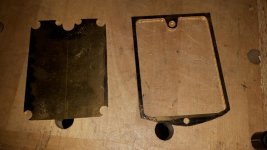
Nach dem Fein-bearbeiten der inneren Kontur (Sägeschnittlinie) des rechten Teiles wurde es auf den Kühler aufgelötet. Die Bearbeitung der äußeren Kontur erfolgte erst nach dem Anbringen. Hier noch vor der Außen-Bearbeitung, nur der aufgelötete „schmale Rahmen“ wurde im Bereich der Lötnaht bearbeitet.
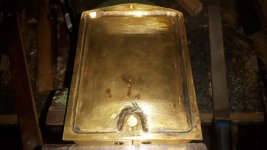
Der vorerst mal fertige Kühler, auf die Längsträger geschraubt, sieht so aus. Für das DIESEL-Logo mit Stern muss ich mir noch etwas einfallen lassen. Diese Teile werden dann aber auch erst nach dem Lackieren angebracht. Tendenziell werden diese / wird das dann schraubbar werden. Ein Loch im Kühler ist dann schnell gebohrt.
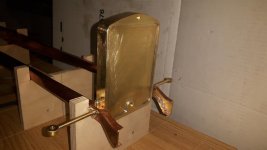
So meine Lieben, das war es schon wieder für heute. Viel Spaß beim lesen und kommentieren.
Bis bald mal wieder.